熔模铸造加压真空吸铸工艺的实例
目前国内许多精铸厂普遍存在精铸件一次成品合格率不高、产品档次低和附加值低的现状。缩孔、浇不足、疏松是熔模铸造常见的铸造缺陷,采用加压真空吸铸工艺浇注导弹发动机叶轮,能消除上述缺陷。采用该工艺生产薄壁件、复杂件和大型精密件的效果也十分显著,具有充型能力强、铝合金铸件的密度高、金相组织细小、均匀,力学性能大大提高。精铸企业要做大做强,除了着力提高工艺过程水平外,同时,必须走工艺创新、装备改进的发展道路。
一、铸件结构分析
某导弹发动机叶轮的结构形状见图1 ,其主体分别由内、外两个圆柱体组成,两个圆柱的壁厚相差不大。圆柱内有两圈叶轮,小圆柱内均布16 条叶片,大圆柱内均布22 条叶片, 叶片形状呈曲面, 叶片厚度为1. 2mm ,叶片的薄截面要求的尺寸精度高,叶面粗糙度Ra≤3. 2 μm ,叶轮高度尺寸为164 mm ,大圆外径为350mm ,铸件单件质量为9kg 。
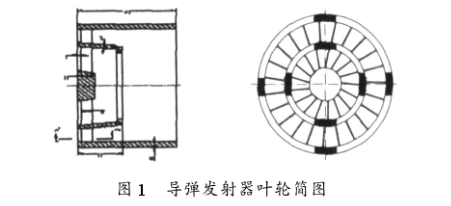
叶轮材料为A356 铝合金,铸件的技术要求除无铸造缺陷外,叶片不允许焊补,每片叶片需100 %经过荧光探伤。该叶轮铸造的最大难点是壁厚不均匀,叶片特别薄,叶片呈隔层分布,数量又多,在完整充型上面临困难。若采用离心浇注,由于叶片曲面的旋角方向不一致,难以实施。常规的重力浇注根本无法保证品质要求,废品率相当高。分析论证认为,必须采用加压吸铸浇注工艺才能满足产品的要求。
二、组树及浇棒
叶轮的蜡模采用低温模料制模,组树方案见图2 。叶轮的上部和底部采用“十字型”横浇道,横浇道与吸铸棒相连。叶轮的内腔有4 根竖立的直浇道,直浇道的一端连接内腔的直径为202 mm 的圆柱平面,另一端连接到上部横浇道上。在叶轮内腔下部中央,有一段82 mm 高,直径为50 mm 的锥形圆柱实体,竖立的直浇道与该锥形圆柱实体平面连接,直浇道(即吸铸棒) 的另一端与上部的横浇道相连。吸铸棒在中心位置“, 十字型”横浇道与它相连成一体,整个模组具有良好的刚性。真空吸铸工艺所用的吸铸专用浇棒(即熔模铸造常用的浇口棒) ,其特点是两端有两个浇杯、两支木柄,浇棒的中间呈正方形或圆形。导弹发动机叶轮在组树前,将吸铸浇棒截成两段,分别焊接在实体锥形圆柱的上、下部。
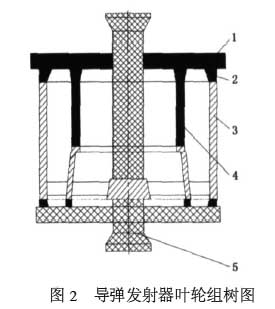
三、制壳及焙烧
制壳采用常规的全硅溶胶结壳工艺,用锆英粉、锆英砂涂制双面层,第3 层开始用莫来粉、莫来砂涂制。此件通常涂制6 层半型壳强度就够了,但是采用加压真空吸铸工艺,其涂层为8 层半。型壳焙烧温度为1 030 ℃,保温时间≥30 min ,然后转移至保温炉,保温温度为540~570 ℃,供连续吸铸用。
四、吸铸及加压
1、加压真空吸铸炉结构
加压真空吸铸炉分为上、下两部分,炉盖板以下属于加压真空吸铸炉的下部(即熔池部份) ,上部为加压真空吸铸炉炉体[1 ] 。
铝合金的熔炼、变质、精炼、调整元素成分、金属液的保温都在下部炉体中完成,待纯净的铝合金液制备好后,将炉盖板盖在熔池上,把经过焙烧和保温的模壳放置好,然后,将加压真空吸铸炉炉体与炉盖板对接密闭合上,这时,加压吸铸前的准备工作结束。
2、加压真空吸铸工艺参数
一次吸铸一组导叶轮模壳; 铝合金液浇注温度为700~730 ℃;型壳浇注温度为530~570 ℃;工作真空度为0. 133 Pa ; 抽真空时间为20~25 s ; 吸铸压力为0. 15 MPa ;吸铸时间为60 s ;吸铸完毕立即加压,加压力为0. 5 MPa ;加压时间为8 min ;最大壁厚的凝固时间为100~110 s ;最小壁厚的凝固时间为30 s ;全部凝固时间为120~150 s。
五、铸件及设备
采用熔模铸造工艺制壳、加压真空吸铸的工艺铸出铝合金导弹发动机叶轮,通过了质量验收,并已稳定地投入批量生产(见图3) ,铸件一次成品合格率达95 %以上。加压真空吸铸炉是自行设计的自制设备,造价低,使用和维护方便,图4 是适合生产中、小件的分别为六支、4 支吸铸管的炉体盖板,金属利用率高,生产效率高,一次能吸铸多件产品。
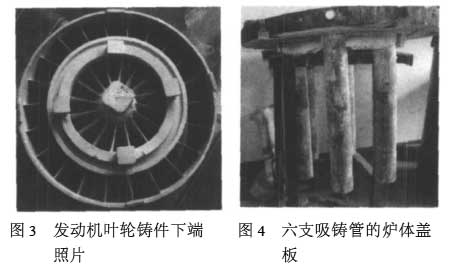
『不是原创,来自于互联网』